SCUBA test facility
Steam bubble condensation is an important phenomenon that is encountered in many industrial and technical applications. Examples are: Mixing type heat exchangers, thermal degasifies, sea water desalination, compact heat exchangers, and safety systems in nuclear power plants: In-containment refueling water storage tank (IRWST, PWR AP1000), suppression pool of passively safe boiling water reactor BWR design, and most important in subcooled boiling that can take place in PWR accidental conditions and BWR normal operation or accidental conditions.
Description

3D Illustration of SCUBA test facility and its components. To the left a picture of the test section with the water aquarium and injection nozzle can be seen.
SCUBA is a test facility for experimental investigation of steam bubble condensation directly injected into flowing subcooled water. The experimental results obtained from the facility are used to get new correlations for heat transfer and improve performance of CFD codes. The test section is a vertical DN100 transparent pipe that allows optical observation of the condensing bubbles using a high speed camera techniques. A large storage tank with electrical heaters provides hot water and a pump circulates the water through the test section. Steam is generated by a small electrical steam generator and is directly injected into the water flow within the test section via different injection nozzles. This allow to change the characteristics of the resulting bubbles: size, initial velocity vector, and deformation. SCUBA has the following flow characteristics (superficial velocities are related to DN100 pipe):
For each injection nozzle a test matrix of 27 measurements are performed at three different water/steam velocities and water temperatures according to the following table:


Measuring Techniques
- High speed camera is the main measuring device that enables to track the condensing bubbles at high time and space resolution (0.3 mm/pixel and up to 1500 frame/s are possible). This allows a detailed observation of the bubble behavior, shape, size, deformation, movement, and even surface structure is revealed.
- Temperatures, pressures, steam and water flow rates are controlled and measured in test section via automated data acquisition system and LabVIEW-based program.
- Self-developed algorithms for image processing allows identification and tracking of bubbles parameters in all recorded images (3000 image corresponding to 2 s of acquisition are recorded for each measurement of the test matrix).
- The program recognizes and detect each condensing bubbles after detachment and tracks its position, relative velocity and diameter along time. As a result, it delivers (Nu,Re) value for each condensing bubble.

Results: Optical Observations/Condensation sequence
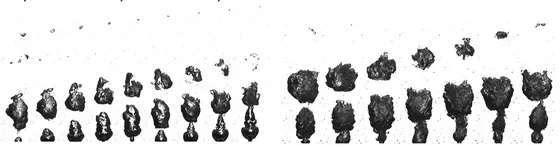
Sequential images of condensing bubble at low-(left image ) and high- (right image ) steam injection velocities.
Results: Optical Observations/ videos
Results: Nu-Re Correlations and bubble diameter along time can be obtained. new correlations are applied into CFD codes for a better simulations.

Results: Void fraction distribution after injection nozzle: as 2D distribution (Steam plumes) or as non-dimensional change along vertical axis
Results: Improvement of CFD simulations/example
- 98°C water temperature , and 0.4 m/s water superficial velocity.
- 4 kg/hour steam inlet through 4 mm vertical nozzle.
- Saturation temperature 104°C.
- Monodispersed bubbly flow with 25 mm diameter.
- Two-resistance phase transfer model.

left plot: Experimental Nusselt number Right plot: standard Ranz-Marshal Nusselt correlation. It can be clearly noticed that the experimental correlations produces the correct shape of the steam flame after the nozzle while standard correlation can not and the steam bubbles reach the end of the pipe.
for more information contact:
Prof. Macián-Juan Rafael macian(at)ntech.mw.tum.de
Dr.-Ing. Suleiman Al Issa issa(at)ntech.mw.tum.de